XTÂ Laser Metal Laser Cutting Machine
Metal laser cutting machines replace traditional mechanical knives with invisible beams of light, and their role in the development of the sheet metal industry is becoming increasingly prominent. They will gradually improve or replace traditional metal cutting process equipment. Their most significant characteristics are high accuracy, fast cutting, not limited to cutting plan limitations, automatic layout saving materials, smooth cuts, and low processing costs. So, what are the main processes and applications of metal laser cutting machines? Next, let’s introduce the common processes and applications of laser cutting machines.
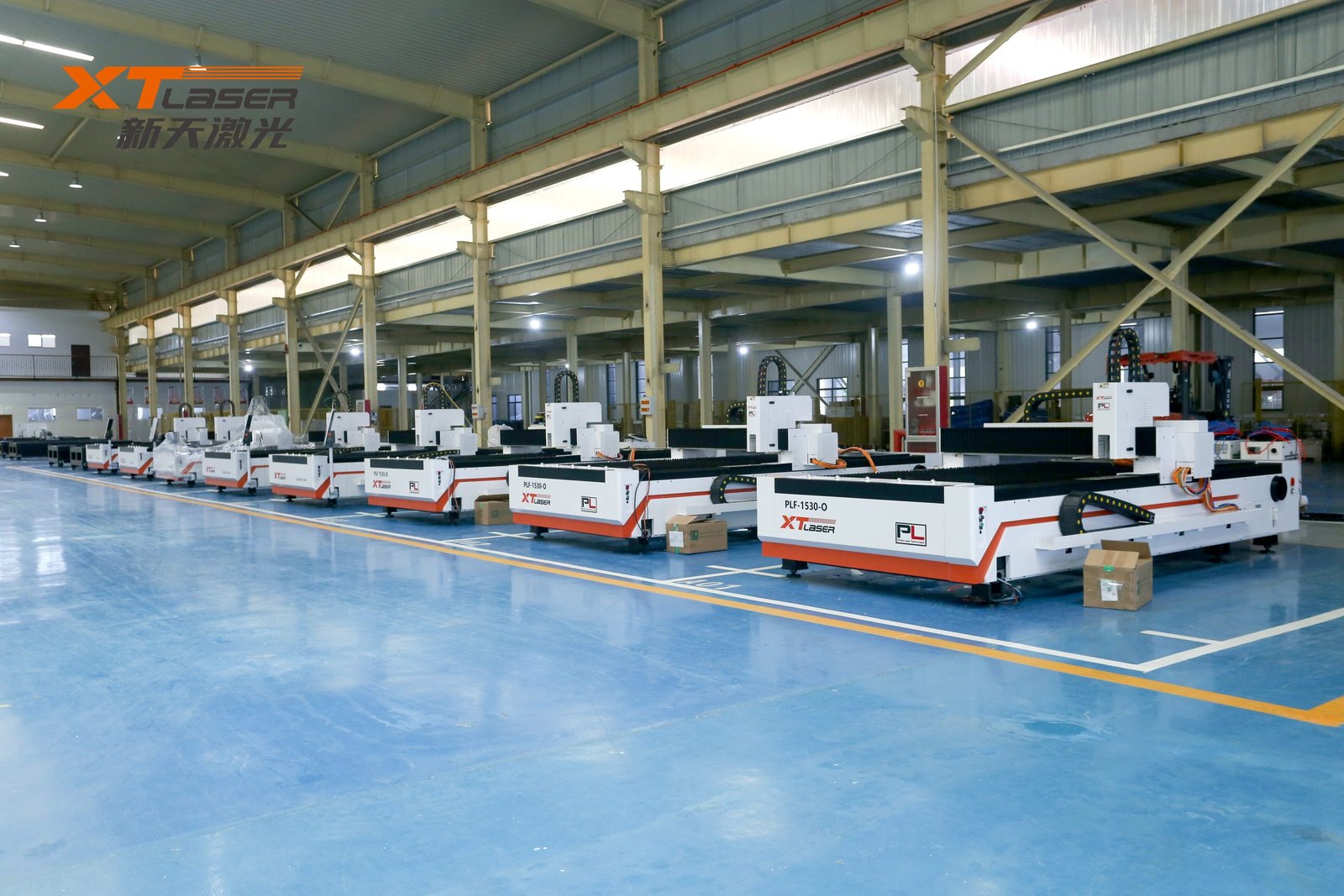
Main processes of metal laser cutting machine
Vaporization cutting
In the process of laser gasification cutting, the speed at which the surface temperature of the material rises to the boiling point temperature is so fast that it is sufficient to avoid melting caused by heat conduction. As a result, some materials vaporize into steam and disappear, while some materials are blown away as ejecta from the bottom of the cutting seam by auxiliary gas flow. This processing is actually only used in very small areas of iron-based alloys.
Melt cutting
In laser melting and cutting, the workpiece is partially melted and the melted material is sprayed out using an airflow. Because the transfer of materials only occurs in their liquid state, this process is called laser melting cutting. Laser melting cutting can achieve non oxidation notches for iron materials and titanium metals.
Oxidative melting cutting (laser flame cutting)
Melting cutting generally uses inert gas. If oxygen or other active gases are replaced, the material is ignited under the irradiation of a laser beam and undergoes a fierce chemical reaction with oxygen to generate another heat source, further heating the material, which is called oxidation melting cutting.
Due to this effect, for structural steel of the same thickness, the cutting rate obtained by this method is higher than that obtained by melt cutting. On the other hand, this method may have poorer notch quality compared to melt cutting.
Control fracture cutting
For brittle materials that are prone to thermal damage, high-speed and controllable cutting through laser beam heating is called controlled fracture cutting. This cutting process can guide the generation of cracks in any desired direction as long as a balanced heating gradient is maintained.
In summary, the processing techniques of laser cutting machines mainly include the following.
Application of Metal Laser Cutting Machine
Application industries: various mechanical manufacturing and processing industries such as rail transit, shipbuilding, automobiles, engineering machinery, agricultural and forestry machinery, electrical manufacturing, elevator manufacturing, household appliances, grain machinery, textile machinery, tool processing, petroleum machinery, food machinery, kitchen utensils and bathroom, decorative advertising, laser external processing services, etc.
Applicable materials: various metal materials such as carbon steel, stainless steel, aluminum alloy, brass, copper, pickled plate, galvanized plate, silicon steel plate, electrolytic plate, titanium alloy, manganese alloy, etc.