XT Laser – Laser Cutting Machine
What are the advantages of laser cutting machines? Why do most metal processing manufacturers now use laser cutting machines? In the current fiber laser cutting machine industry, major manufacturers are secretly playing games and facing numerous risks. Success leads to success, while failure leads to disappearance in the market. Today, with a focus on product quality, the demand for customers who can buy laser cutting machines is changing. The personalized demand for equipment is being stimulated by the market, and the ease of operation of equipment has become one of the purchasing factors. Next, let’s analyze the applications and advantages of laser cutting machines.
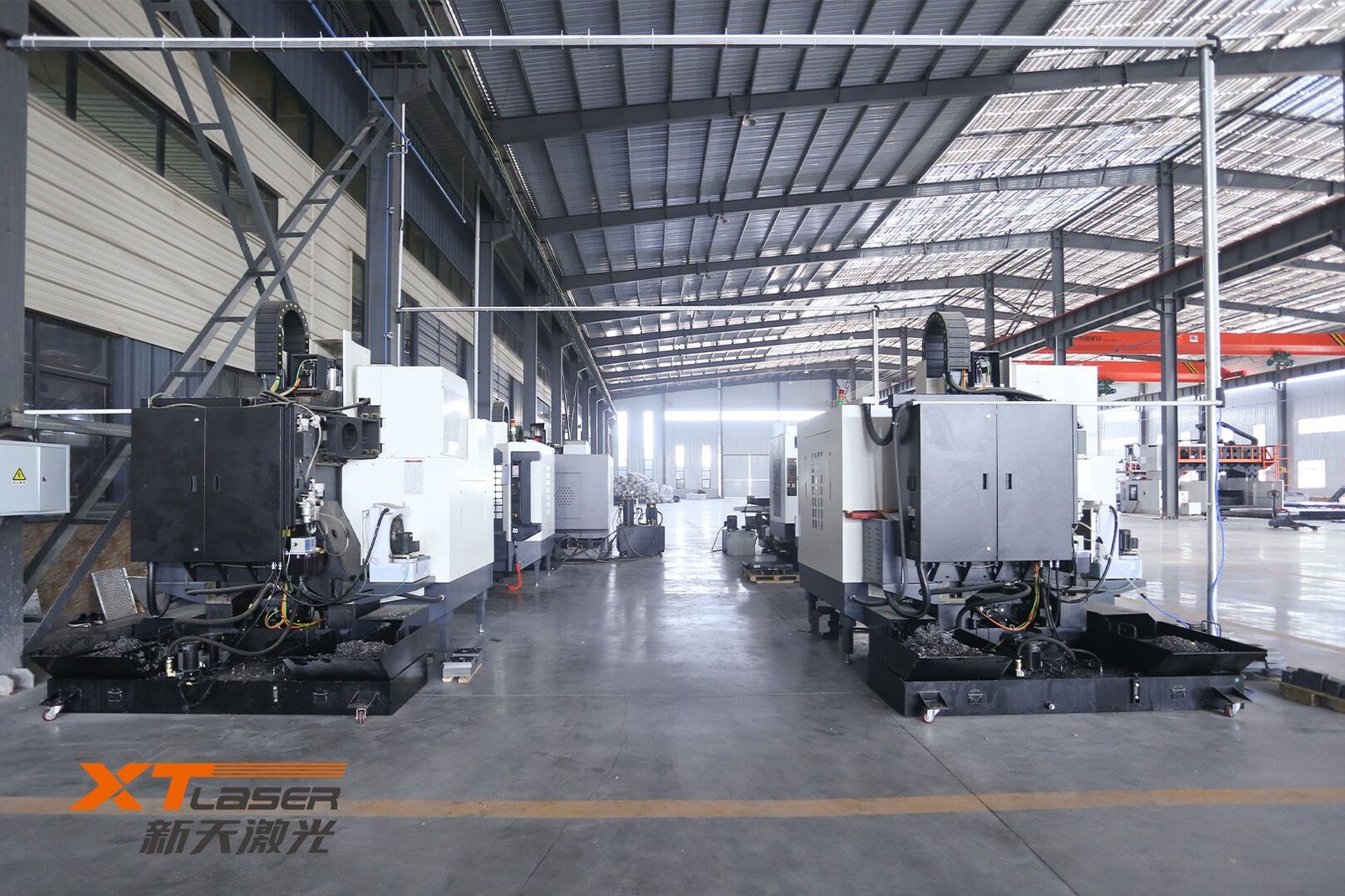
A laser cutting machine uses a focusing mirror to focus the laser beam on the surface of a material, causing the material to melt. At the same time, compressed gas coaxial with the laser beam is used to blow away the melted material, causing the laser beam to move relative to the material along a certain trajectory, thereby forming a certain shape of the cutting seam.
Application Fields of Laser Cutting Machines
Various machinery manufacturing and processing industries include machine tools, engineering machinery, electrical switch manufacturing, elevator manufacturing, grain machinery, textile machinery, locomotive manufacturing, agricultural and forestry machinery, food machinery, special vehicles, petroleum machinery manufacturing, environmental protection equipment, household appliance manufacturing, large motor silicon steel sheets, etc.
Significant advantages of laser cutting machines
1. High accuracy: positioning accuracy up to 0.05mm, repeated positioning accuracy up to 0.02mm
2. Narrow slit: The laser beam is focused into very small light points, achieving a high power density at the focal point. The material is quickly heated to the point of vaporization, and holes are formed by evaporation. As the beam of light moves linearly with the material, the holes continuously form narrow slits. The width of the incision is generally 0.10-0.20mm.
3. Smooth cutting surface: The cutting surface is free of burrs, and the surface roughness of the incision is generally controlled within Ra12.5.
4. Fast speed: The cutting speed can reach 10m/min, and the maximum positioning speed can reach 70m/min, which is much faster than the speed of wire cutting.
5. Good cutting quality: non-contact cutting, with minimal heat impact on the cutting edge and almost no thermal deformation of the workpiece, completely avoiding edge collapse formed during material punching and shearing. Generally, there is no need for secondary processing for the cutting seam.
6. No damage to the workpiece: The laser cutting head will not come into contact with the material surface, ensuring that the workpiece is not scratched.
7. Not affected by the hardness of the material being cut: Laser can process steel plates, stainless steel, aluminum alloy plates, hard alloys, etc., and can perform deformation free cutting regardless of the hardness.
8. Not affected by the shape of the workpiece: Laser processing has good flexibility, can process any shape, and can cut pipes and other irregular materials.
9. Saving mold investment: Laser processing does not require molds, does not require mold consumption, does not require mold repair, saves mold replacement time, thus saving processing costs and reducing production costs, especially suitable for processing large products.