XT Laser-laser cutting machine
The laser source has a decisive influence on the productivity of the laser cutting system. However, high profits do not come from laser power alone. The perfect fit of the whole system is also crucial.
Not all laser cutting is equal. Even today, with countless innovations in technology, there are significant differences between corresponding machines. The customer’s position is beyond doubt: they need a system that can produce high-quality cutting parts at the lowest cost, and the system must be highly available in order to complete the work within the predetermined time limit. In this way, you can process as much work as possible per unit time, so as to recover the investment in the system in the shortest time. In short: the higher the productivity of your laser cutting system, the more profits you can make from it. An important factor affecting the productivity of laser cutting system is the laser source used in the system.
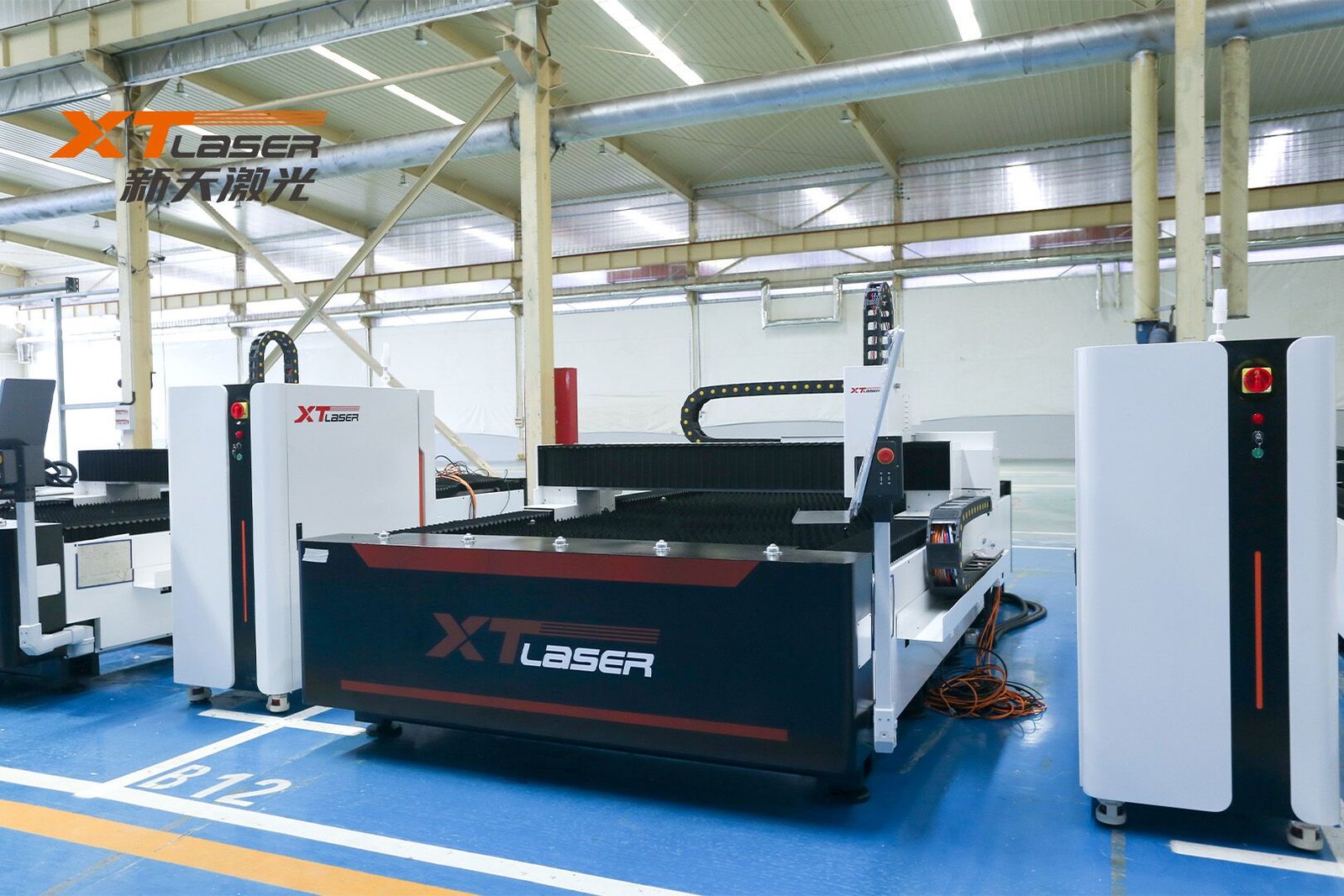
Interaction is the key.
The newly developed perforation method, Controlled Pulse Perforation (CPP), represents the highest performance requirements of laser pulses. CPP can reduce the cutting time by half when processing plates with thickness of 4 to 25 mm. The processing process is divided into two stages, the first is pre-piercing. Keep a large distance between the cutting head and the plate to prevent excessive contamination of the nozzle and lens. Then reduce the spacing and complete the whole perforation. When the perforation is completed, the sensor on the cutting head detects the precise point according to the reflected light and generates the corresponding signal. Then the system immediately starts the cutting process. This processing process not only saves time, but also keeps the hole diameter at a minimum of 1mm on a 10mm thick plate. In addition, almost no stain is visible on the machined surface. At the same time, CPP greatly improves the processing safety of the machine tool.
The introduction of zero puncture time requires the maximum reliability of the laser source. Even at the required point, it must be able to accurately increase and reduce the power. This is no longer a perforation process, but a direct cutting process without time loss, which is applicable to materials up to 8 mm thick. How to move the cutting head to the cutting mark in an arc. Once in place, the system starts cutting immediately. The green dashed part is fully parameterized. At the same time, the actual cutting parameters are converted immediately at the starting point (3) of the contour line, so that the cutting process can be carried out according to these parameters. Then the cutting head moves to the next contour to be cut in an arc. Compared with the traditional piercing method, the consistent use of this method can reduce the cutting time of the workpiece cutting torch by up to 35%.
Laser solutions.
CO2 gas is used as the active material of the laser. Because this kind of laser has not only high output power in industrial applications, but also many other advantages, such as the best laser beam quality, reliability and many other advantages, such as high laser beam quality, reliability and compact design. The laser light source uses direct current (DC) to activate with CO2 gas, and its power can be up to 5.2 kW. The new high power laser adopts a different method: inject energy through the electrode installed outside the ceramic tube, and the ceramic tube contains gas. In this way, energy is released from the electrode in the form of high-frequency wave, which is why this method is called high-frequency activation (or HF activation for short).
Generally speaking, users can benefit from improving the laser power in the following ways: minimize the puncture time, which translates into shorter workpiece cutting time, and minimize the time, which translates into shorter workpiece cutting time, so as to achieve higher and profitable workpiece throughput. Since not all workpieces must be produced at maximum power, the laser power can be stored in the reserve to improve the process safety of the whole system. The maximum plate thickness limit is increased, for example, stainless steel can reach 25 mm, and aluminum can reach 15 mm. This means that the work that users could not complete before can now be completed. In addition, the cutting performance is significantly improved for carbon steel above 6mm and stainless steel above 4mm. Specifically, within the dynamic limit of the system, more laser power is converted into higher feed rate. In fact, it is the increase of feed speed that leads to the reduction of workpiece cutting time and the increase of output.
However, please note that high power does not necessarily mean high profit of laser cutting machine. If the system solution cannot transform this power, it will not help. If the laser cutting machine laser is too expensive, it will not be able to achieve higher profits. Generally, when it comes to laser light source, people first think of its excellent efficiency, high reliability, extremely low power consumption and lowest operating cost. However, the operating cost of this kind of laser is still higher than that of low power laser, mainly due to its higher energy requirements. From the perspective of gross profit rate of typical workpieces, only “appropriate” workpieces combination can achieve corresponding profits, and this combination mainly refers to the processing of medium and thick plates or stainless steel. On the other hand, data from major sheet metal suppliers show that sheet metal processing of 2 to 6 mm is the most important and important in the factory, surpassing all other conventional steel products. Therefore, greater attention must be paid to the system scheme rather than one-sided pursuit of laser power maximization.
To sum up.
When determining the correct laser power for the system investment, it is necessary to carefully check the actual system application field. In order to make full use of the system, the system and the laser light source should be from the same supplier. In addition to highly authoritative consulting services, the supplier should also be able to provide a wide range of high-quality systems and laser light sources.